Central Plant Monitoring
Take control of your plant’s performance today with predictive analytics and smart software solutions. High condenser water temperatures and flow issues may be formidable adversaries, but with the right tools at your disposal, they become manageable challenges on the path to operational excellence.
A University’s Central Plant is the Beating Heart of all Campus Infrastructure
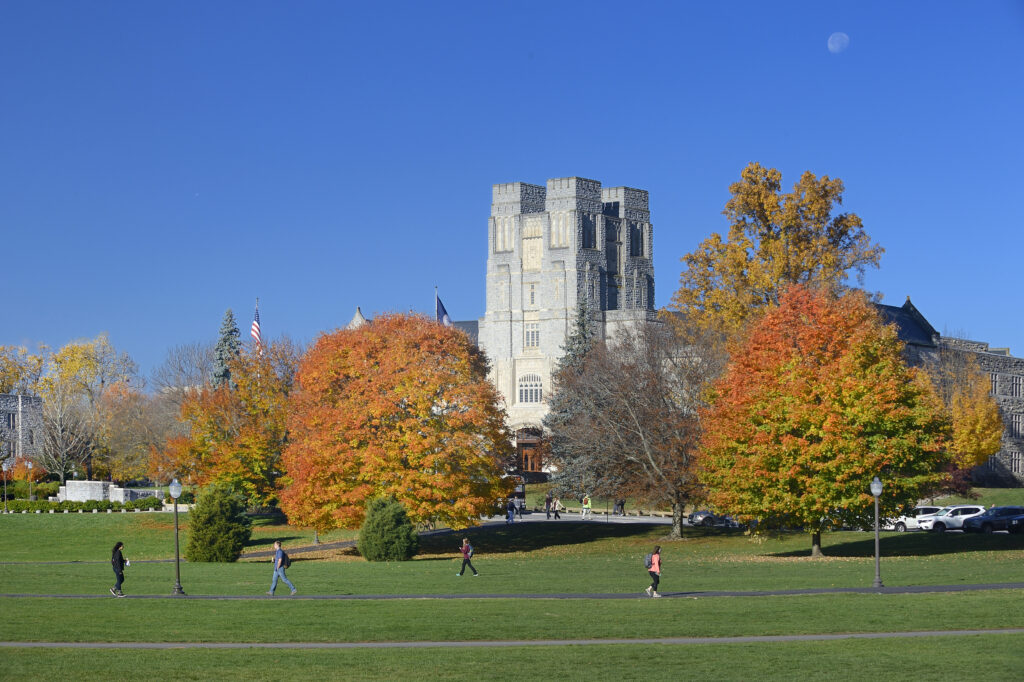
SCADA
The plant’s assets produce hot water, steam, and chilled water to provide space heating and air conditioning for connected buildings. The plant is controlled by operators and a SCADA platform that ensure the university’s energy needs are met. The SCADA platform’s sole function is control; it is not designed to detect inefficiencies, identify asset degradation, or optimize performance. DSA’s WatchPost monitoring platform is specifically designed for these tasks. It works alongside your SCADA to provide decision support information to your operations staff. The WatchPost platform also widens data access to other university stakeholders in a secure way by separating the functions of control and monitoring.
Data-Driven Predictive Insights: Our software leverages end-device time series data to provide predictive insights, helping central plant operators foresee and proactively address operational challenges.
Complementary Solution: Unlike traditional SCADA and DCS systems, our software serves as a valuable complement, enhancing the capabilities of your existing infrastructure.
Operational Optimization: Unlock the power of data-driven decision-making to optimize your central plant’s performance, reducing downtime and improving overall efficiency.
Proactive Issue Forecasting: Stay one step ahead with our solution’s ability to forecast potential issues, enabling timely interventions and minimizing disruptions.
Customized Adaptation: Our software is tailored to seamlessly integrate with your central plant setup, providing a unique solution that aligns with your specific operational needs.
Cost-Effective: Achieve significant operational cost savings by maximizing efficiency, extending equipment lifespan, and minimizing unplanned maintenance.
Streamlined Monitoring: Experience streamlined central plant monitoring that empowers your team to make data-backed decisions for better outcomes.
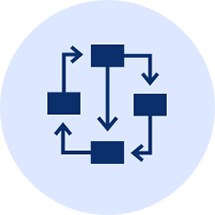
By addressing these issues promptly, you not only reduce the risk of costly repairs and downtime but also extend equipment lifespan and maximize overall energy efficiency. It’s a holistic approach to central utility plant management that pays dividends in cost savings, reliability, and peace of mind.
Forecasting and Effective Dispatch of Assets
Low Delta T Syndrome: This occurs when the temperature difference between the chilled water supply and return is lower than optimal. It can indicate inefficient heat transfer and reduced chiller efficiency.
- Solution: Monitor and optimize the temperature differentials between the supply and return water to maintain efficient chiller operation.
Chiller Cycling: Frequent on/off cycling of chillers can lead to increased wear and tear, reduced efficiency, and higher energy consumption.
- Solution: Implement intelligent chiller dispatch strategies to minimize cycling and maximize chiller efficiency.
Flow Rate Imbalances: Uneven flow rates through the chilled water system can result in inefficient cooling and reduced chiller performance.
- Solution: Monitor flow rates and use control strategies to balance flow through different parts of the system.
Pressure Fluctuations: Variations in system pressure can indicate problems with pumps, valves, or blockages that affect overall system performance.
- Solution: Continuously monitor and control pressure levels to ensure stable and efficient operation.
Temperature Extremes: Extremely high or low temperatures in the system can lead to equipment damage, reduced efficiency, and safety concerns.
- Solution: Implement temperature monitoring and control to maintain the desired operating range.
Energy Demand Peaks: Sudden spikes in energy demand can result in higher utility costs and may strain the electrical infrastructure.
- Solution: Use predictive analytics to anticipate demand peaks and optimize energy usage accordingly.
Equipment Failures: Predictive maintenance can help identify potential equipment failures before they occur, preventing costly downtime and repairs.
- Solution: Implement predictive maintenance based on data analysis to identify and address equipment issues early.
Energy Efficiency: Track and optimize the overall energy efficiency of the central plant to reduce operational costs and environmental impact.
- Solution: Utilize data analytics to continuously improve energy efficiency by adjusting system parameters and settings.
Water Quality: Monitor water quality to prevent issues such as scale buildup and corrosion, which can affect chiller performance and lifespan.
- Solution: Implement water treatment and monitoring to maintain optimal water quality.
Environmental Compliance: Ensure that the plant operations comply with environmental regulations regarding emissions, refrigerants, and waste disposal.
- Solution: Use data monitoring and reporting to track and manage environmental compliance.
High Condenser Water Temperatures: Preventing Costly Downtime
In a central utility plant, high condenser water temperatures can be a ticking time bomb, waiting to disrupt operations and incur substantial costs. When condenser water temperatures rise beyond acceptable levels, it places an immense strain on chillers, decreasing their efficiency and increasing the risk of overheating. Left unaddressed, this issue can lead to a chiller tripping offline, causing downtime, maintenance headaches, and increased energy expenses.
However, there’s a solution at hand – specialized software designed to keep your operations running smoothly. This cutting-edge software goes beyond basic temperature monitoring, employing advanced analytics and predictive algorithms to detect rising condenser water temperatures early. By continuously analyzing temperature data and comparing it against predefined thresholds, the software identifies anomalies that signal potential issues.
The real magic happens when these anomalies are detected promptly. The software not only alerts operators to impending problems but also provides actionable recommendations for mitigation. Whether it’s adjusting flow rates, optimizing chiller operation, or identifying equipment malfunctions, the software equips your team with the knowledge and tools to prevent chiller downtime and maintain optimal cooling conditions.
With this proactive approach, you not only save on costly emergency repairs but also maximize chiller efficiency and extend equipment lifespan. Say goodbye to unexpected downtime and hello to a more efficient and cost-effective central utility plant, all thanks to the power of predictive analytics and smart software solutions. Don’t let high condenser water temperatures catch you off guard – take control of your plant’s performance today.
Complex Data Analysis
Central utility plants generate vast amounts of data from various sensors and equipment. While SCADA and DCS systems excel at real-time data acquisition and basic control, they often lack the sophisticated data analysis capabilities needed for predictive insights. A dedicated software solution employs advanced analytics and machine learning algorithms to uncover hidden patterns and anomalies within the data, enabling early issue detection and forecasting.
Proactive Problem Resolution
Traditional SCADA and DCS systems are primarily reactive, focusing on immediate control and monitoring. In contrast, a specialized software solution takes a proactive approach by analyzing historical and real-time data to predict potential issues before they escalate. This enables operators to intervene early, preventing downtime, reducing maintenance costs, and optimizing energy consumption.
Customization and Adaptability
A central utility plant’s needs can be highly specific and may evolve over time. Unlike SCADA and DCS systems, which have predefined functionalities, a dedicated software solution is highly adaptable and can be customized to suit the unique requirements of the plant. It can integrate seamlessly with existing infrastructure and evolve alongside changing operational needs.
Where WatchPost Comes In
Anomaly Detection: Central utility plants often face issues that are subtle and challenging to identify using traditional systems. A specialized software solution excels at anomaly detection, recognizing deviations from expected behavior within the data. It can flag issues like low Delta T syndrome, flow rate imbalances, and inefficient chiller cycling, which may go unnoticed by SCADA and DCS systems.
Optimization and Efficiency: While SCADA and DCS systems maintain basic control functions, they may lack the optimization capabilities necessary for maximizing efficiency and reducing operating costs. A dedicated software solution continuously optimizes plant operations, adjusting parameters based on data-driven insights to achieve the highest possible efficiency.
Predictive Maintenance: Predictive maintenance is crucial for preventing equipment failures and minimizing downtime. Specialized software can predict when equipment is likely to fail and recommend maintenance actions, whereas SCADA and DCS systems typically lack these predictive maintenance features.
Data Integration: Central utility plants often have diverse equipment and data sources. A dedicated software solution can integrate data from various sources, providing a holistic view of plant operations. SCADA and DCS systems may be limited in their ability to consolidate and analyze data from different systems and sources.
Long-Term Cost Savings: Investing in a predictive and forecasting software solution can lead to significant long-term cost savings. By preventing unplanned downtime, optimizing energy usage, and extending equipment lifespan, the software can pay for itself many times over.
High Condenser Water Temperatures: In a central utility plant, elevated condenser water temperatures can lead to reduced chiller efficiency, potential equipment damage, and compromised cooling performance. While traditional SCADA and DCS systems may provide basic temperature monitoring, a dedicated software solution offers advanced analytics to detect and address high condenser water temperatures proactively. By continuously monitoring temperature data and comparing it against established thresholds, the software can alert operators to potential issues and recommend adjustments to maintain optimal cooling conditions. This level of precision ensures the efficient operation of the entire cooling system, preventing overheating and minimizing energy consumption.
Optimizing Central Utility Plant Performance: Addressing High Condenser Water Temperatures and Flow Issues
In the complex world of central utility plants, efficient operation is paramount. Yet, lurking within the intricate web of chillers, pumps, and cooling towers are challenges that, if left unattended, can disrupt operations and inflate costs. High condenser water temperature has already been discussed above. Now let’s discuss the other issue, condenser water flow issues.
Condenser Water Flow Issues: Similarly, imbalances or fluctuations in condenser water flow rates can wreak havoc. Uneven flow distribution can lead to inefficient cooling and hinder chiller performance, causing operational headaches and increased maintenance needs.
But here’s the good news: a specialized software solution is the linchpin in your battle against these challenges. This advanced software is not merely a passive observer; it’s your plant’s proactive guardian.
Using advanced analytics and predictive algorithms, the software continuously monitors temperature and flow data. It identifies anomalies early, well before they escalate into emergencies. When high condenser water temperatures or flow issues are detected, the software doesn’t just sound the alarm—it offers actionable recommendations for mitigation.
Operators receive guidance on precisely how to recalibrate the system, adjust flow rates, optimize chiller operation, or identify and resolve equipment malfunctions. It empowers your team to act swiftly, heading off potential disasters before they materialize. Downtime becomes a rarity, and operational efficiency soars.